Plastic 3D Printing
Possibilities
A PROCESS FOR EVERY SOLUTION
Processes
0
Layer Thickness
from 0 mm
Wall Thickness
from 0 mm
Processes
0
Layer Thickness
from 0 mm
Wall Thickness
from 0 mm
NEW at HENNgineered: HPS: Next-level technology
We are one of the first companies in the world to use the new Hybrid PhotoSynthesis technology, which combines the strengths of stereolithography (SLA) and digital light processing (DLP). This enables up to 20 times faster printing speeds compared to conventional SLA processes. Thanks to the introduction of HPS technology, HENNgineered is able to produce larger and more complex components without having to compromise on precision and functional properties – and with a unique surface quality.
All the advantages of HPS technology over existing 3D printing processes at a glance:
- Higher speed
- Size and volume flexibility
- First-class quality and exceptional throughput rate
- Outstanding surface finish
- Wide range of materials for the highest requirements
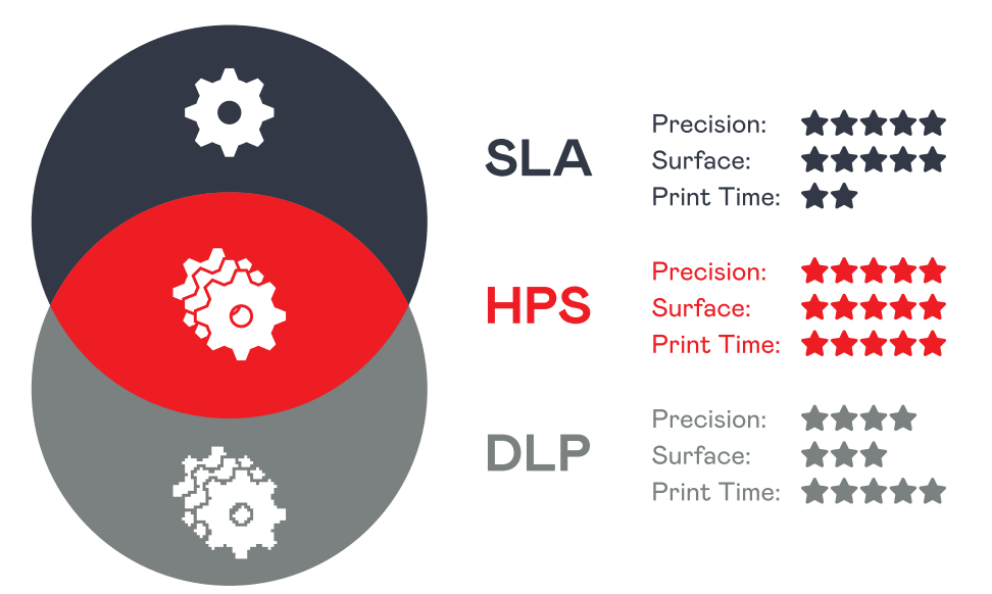
USE CASES
Technology
OVERVIEW MADE EASY: PLASTIC 3D PRINTING
Stereolithography (SLA/STL)
Stereolithography is the oldest 3D printing process and has been used since the 1980s to cure objects using resin (photopolymer) with a UV laser. Watershed XC 11122 photopolymer is well suited for building light guides, viewing windows and master models for vacuum casting or PA casting. It enables precise 3D prints with smooth surfaces that meet optical and haptic requirements. We also offer:
- Heat deflection temperature of 292 °C HDT
- Optical transparency
- Medical approval ISO 10993-5, ISO 10993-10, USP VI
- Biocompatibility
Selective Laser Sintering (SLS)
This process is the most widely used because it can produce very robust and resilient parts. It is a powder bed process in which a laser fuses the powder applied to a substrate plate, layer by layer, until a solid 3D body is formed. Unlike metal printing, no support structures are required between the parts. This results in more space, making the process maximally efficient and thus cost-effective. This method is ideal for resilient parts that do not require a high optical or haptic standard. We offer the series materials PA 11, PA 12 and PA 6 each with and without glass filling.
Polyjet Process
The special feature of the polyjet process (also known as: Multijet Modelling, MJM) is the high resolution of 0.016 millimetres per construction stage and the associated ability to build components with very thin walls that are visually and haptically appealing – ideal for making small master models for vacuum casting. To achieve this, 960 material nozzles jet out artificial photopolymer plastic, which is immediately solidified by powerful UV lights. Full-colour models with multi-colour printing and realistic surfaces can be produced in this way.
Multijet Fusion (MJF)
Only on the market since 2017, this is a very new alternative to SLS. Although this process also uses a powder bed, chemicals are used to mark the areas that are to be fused with strong heat lamps. The biggest advantage over SLS is that this process can produce closed, homogeneous microstructures like those of an injection-moulded part. It is ideally suited to producing small batches, as well as visual and functional samples without high optical and haptic demands. This process is comparatively inexpensive. We work with the series material PA 12, with and without glass filling.
Fused Deposition Modelling (FDM)
The starting material is thermoplastic plastic wire (filament), which is unwound from a spool and fed into your heated nozzle. There, semi-fluid plastic filaments are fused together to form a solid body. The main advantage of this process is the diverse choice of materials – meaning you can always use the original material that will later be used for the series. Of particular interest here are high-temperature materials such as Ultem or continuous fibres made of carbon or glass fibre, which are highly resistant. Perfect for jigs and fixtures. The process also offers:
- High temperature resistance at 216 °C HDT
- Glass or carbon fibre filling with a bending strength of 142 MPa
- Tensile strength of 87 MPa
- Self-extinguishing properties
- Rail approval EN 45545, NFPA 130, SMP 800-C
- Aviation approval FAR 25.853
- Chemical resistance
- Biocompatible, autoclavable and sterilisable
- Suitable for food contact
- Electrostatically dissipative
- Choice of various lightfast solid colours
- Washable and water soluble
Digital LIght Processing (DLP)
The starting point for this process is a basin filled with a photopolymer. This plastic reacts to the influence of light and solidifies after a certain exposure time. A 3D model previously created by CAD is projected layer by layer onto the surface of the liquid plastic with the help of a projector. Under the influence of light, the corresponding regions solidify. Afterwards, the solidified layer is pushed upwards by the height of one layer by a moving platform. Liquid photopolymer recollects under the first layer, which is once again exposed to light. Bit by bit, a complete model is created. After the printing process is completed, the model is removed from the tank and exposed to light in an exposure chamber. This achieves the full and permanent curing. Further properties are:
- Tensile modulus of 4500 MPa
- Tensile strength of 97 MPa
- Heat deflection temperature of 292 °C HDT
- Self-extinguishing according to UL 94 V0
- Medical approval ISO 10993-5, ISO 10993-10
- Biocompatibility
- Elastomeric character with 47 or 75 Shore A